300 Level 301 - Chapter 4
Friction Loss Coefficients and How to Use Them
Although it’s convenient to use a Rule of Thumb (link to 6. Table – Estimating Total Dynamic Head) to ‘guesstimate’ friction loss in smaller features, calculating exactly what the friction head is in any system is not difficult. The tool that makes this possible is the Friction Loss Coefficient Chart, which provides a coefficient of friction loss for any given size and length of pipe, as well as a handy way to add up the friction caused by fittings. Using the Chart, you’ll know exactly how much additional head your system’s plumbing adds to the actual height of the waterfall, and what it subtracts from your flow. If you’re designing a system, you’ll be able to maximize pump output by using the Chart to plan out the size of the plumbing and the number of fittings. Let’s start with a “typical” water feature like the one we looked at in Advantages of Redundancy, where our hypothetical water feature needed around 3900 gallons per hour at 5 feet of head. Let’s also suppose that we’ll need 25’ of PVC Flex Pipe, with a 90 degree elbow, a male/female adapter and a check valve. The pumps listed all have 1½” outlets, so let’s see what happens if we use 1½” plumbing. Going to the Chart we’ll look down the first column listing Gallons Per Minute (GPM). Since 3900 GPH is 65 GPM, halfway between 60 GPM at 21.6 and 70 GPM at 28.8 is around 25. This number represents the friction generated at that flow through 100 feet of pipe, in feet of head. That is, running 3900GPH through 100 feet of 1½” Flex, flat on the ground, is the same work for the pump as lifting a column of water 25 feet in the air! That’s a lot of friction! Now we already said we only needed 25’ of tubing, one quarter of the 100-foot coefficient, so the actual friction loss would in our 25 feet of 1½” PVC only be one quarter of the 25 feet of head, a little over 6’ of additional head – but what about the fittings? The easy way to add in the friction losses caused by fittings is to assign them a head value equivalent to a length of tubing, which is what our Fitting Friction Loss Chart does. A 90 degree elbow in 1½” PVC adds 7.5 feet to the 25 feet of tubing, the male/female adapter and the check valve another 3.5 and 15.2, for a total equivalent length of 51.2 feet. The actual friction head in the tubing plus the fittings is 51.2/100ths, or about 13 feet of head, that has to be added to the actual height of 5’. Using 1½” plumbing you would need a pump that delivers 3900 GPH at 18’ of head. That’s a pretty big pump.
Let’s see what would happen if we change the tubing to 2” PVC…. The 2” fittingsadd 8.6, 4.5 and 19.1 to the 25’ length of tubing, for a total of 57.2, again a little more than ½ of the friction coefficient for the 100’ of 2” – BUT… what is that coefficient? Halfway between 7.43 and 9.88, and half of that is less than 5 feet of friction head, so the total head ends up under 10 feet instead of 18. Going to the Comprehensive Pump Chart we find we’d need an A-21, drawing 1060 watts, or at least a PAF75 at 900 Watts to deliver the required flow at 18’ of head through 1½” tubing, but simply by installing 2” tubing we could downsize to a TW6000 that delivers the same flow at 10’ of head yet draws only 495 Watts, half as much power. How much of a savings is that? Well, even at only 10 cents a kilowatt/hour, 565/1000 x $0.10 x 24 hours a day x 30 days equals a savings of over $40 dollars every month on your electric bill.
Now does it make sense to upsize your tubing? The following Tubing Flow Rates Chart will serve as a guide to maximizing plumbing efficiency.
TUBING FLOW RATES
The fluid flow velocities in water systems should not exceed certain limits to avoid noise and damage to pipes and fittings. The Plastic Pipe and Fittings Association (PPFA) recommends a maximum flow-rate velocity of 5 to 8 feet per second (fps) through Schedule 40 PVC pipe, with the highest efficiencies and lowest risk of damage at about 5 fps max for larger pipe sizes. Besides possible pipe failure, higher flows create huge resistance to water flow, necessitating higher power requirements and higher operating costs. The table below should be used as:
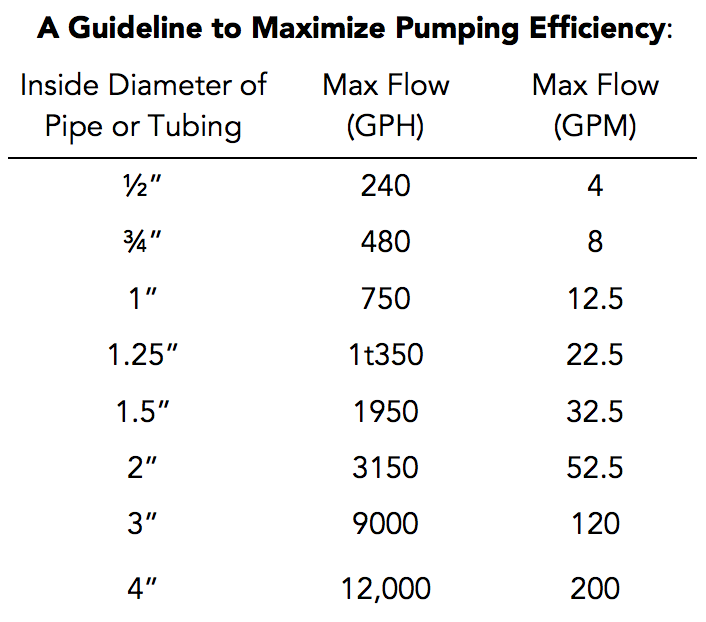
Although it’s convenient to use a Rule of Thumb (link to 6. Table – Estimating Total Dynamic Head) to ‘guesstimate’ friction loss in smaller features, calculating exactly what the friction head is in any system is not difficult. The tool that makes this possible is the Friction Loss Coefficient Chart, which provides a coefficient of friction loss for any given size and length of pipe, as well as a handy way to add up the friction caused by fittings. Using the Chart, you’ll know exactly how much additional head your system’s plumbing adds to the actual height of the waterfall, and what it subtracts from your flow. If you’re designing a system, you’ll be able to maximize pump output by using the Chart to plan out the size of the plumbing and the number of fittings. Let’s start with a “typical” water feature like the one we looked at in Advantages of Redundancy, where our hypothetical water feature needed around 3900 gallons per hour at 5 feet of head. Let’s also suppose that we’ll need 25’ of PVC Flex Pipe, with a 90 degree elbow, a male/female adapter and a check valve. The pumps listed all have 1½” outlets, so let’s see what happens if we use 1½” plumbing. Going to the Chart we’ll look down the first column listing Gallons Per Minute (GPM). Since 3900 GPH is 65 GPM, halfway between 60 GPM at 21.6 and 70 GPM at 28.8 is around 25. This number represents the friction generated at that flow through 100 feet of pipe, in feet of head. That is, running 3900GPH through 100 feet of 1½” Flex, flat on the ground, is the same work for the pump as lifting a column of water 25 feet in the air! That’s a lot of friction! Now we already said we only needed 25’ of tubing, one quarter of the 100-foot coefficient, so the actual friction loss would in our 25 feet of 1½” PVC only be one quarter of the 25 feet of head, a little over 6’ of additional head – but what about the fittings? The easy way to add in the friction losses caused by fittings is to assign them a head value equivalent to a length of tubing, which is what our Fitting Friction Loss Chart does. A 90 degree elbow in 1½” PVC adds 7.5 feet to the 25 feet of tubing, the male/female adapter and the check valve another 3.5 and 15.2, for a total equivalent length of 51.2 feet. The actual friction head in the tubing plus the fittings is 51.2/100ths, or about 13 feet of head, that has to be added to the actual height of 5’. Using 1½” plumbing you would need a pump that delivers 3900 GPH at 18’ of head. That’s a pretty big pump.
Let’s see what would happen if we change the tubing to 2” PVC…. The 2” fittingsadd 8.6, 4.5 and 19.1 to the 25’ length of tubing, for a total of 57.2, again a little more than ½ of the friction coefficient for the 100’ of 2” – BUT… what is that coefficient? Halfway between 7.43 and 9.88, and half of that is less than 5 feet of friction head, so the total head ends up under 10 feet instead of 18. Going to the Comprehensive Pump Chart we find we’d need an A-21, drawing 1060 watts, or at least a PAF75 at 900 Watts to deliver the required flow at 18’ of head through 1½” tubing, but simply by installing 2” tubing we could downsize to a TW6000 that delivers the same flow at 10’ of head yet draws only 495 Watts, half as much power. How much of a savings is that? Well, even at only 10 cents a kilowatt/hour, 565/1000 x $0.10 x 24 hours a day x 30 days equals a savings of over $40 dollars every month on your electric bill.
Now does it make sense to upsize your tubing? The following Tubing Flow Rates Chart will serve as a guide to maximizing plumbing efficiency.
TUBING FLOW RATES
The fluid flow velocities in water systems should not exceed certain limits to avoid noise and damage to pipes and fittings. The Plastic Pipe and Fittings Association (PPFA) recommends a maximum flow-rate velocity of 5 to 8 feet per second (fps) through Schedule 40 PVC pipe, with the highest efficiencies and lowest risk of damage at about 5 fps max for larger pipe sizes. Besides possible pipe failure, higher flows create huge resistance to water flow, necessitating higher power requirements and higher operating costs. The table below should be used as: